Shot Peening FAQs
Home / Shot Peening FAQs
Shot peening enhances the surface of the part by replacing potential tensile stress with a surface compressive residual stress.
No. Shot peening’s primary function is to enhance the fatigue life of a part, whereas sand blasting or abrasive grit blasting is used to clean or prepare a part for a coating.
Compressive stress is the stress applied to materials resulting in their compaction (decrease of volume). When a material is subjected to compressive stress, the material is under compression. Shot peening produces compressive stress on the surface. This compression helps the part resist cracking, in turn extending the service life of the component.
No. Shot peening actually induces a thin layer of compressive stress on the surface of the part which replaces surface tensile stress. Stress relieving is a heat treatment process to remove both tensile and compressive stresses.
X-ray diffraction testing is a way to measure the stress in a material. This allows one to quantify how much stress is in an area of a part so the actual amount of stress can be measured for testing purposes. In order to determine the depth of the compressive stress, multiple x-ray diffraction measurements are made as layers of the test coupons are electro-polished away.
A saturation curve should be run whenever intensity checks fail, after significant machine maintenance, any lif- changing event, or at least every year.
A saturation curve is a standardized method used to determine shot stream intensity by exposing Almen strips to a shot stream for varying amounts of time with all other parameters fixed. Adjusting the exposure can be varied in time, passes, federates, cycles, etc. The arc height of the Almen strips are plotted versus exposure time. A best fit curve is generated through the points. The saturation point is the first point on the saturation curve (not necessarily a data point) where the arc height increases by 10% when the peening time is doubled; this is also the shot stream intensity at that location.
No. Saturation point is calculated using the saturation curves, and coverage can only be evaluated by shot peening and visually inspecting an actual part. Coverage will occur much quicker on an aluminum part than on a hardened steel part.
No. The intensity can only be determined by a saturation curve. Since the time to shot peen a part to the proper coverage may take a different amount of time, the arc heights achieved at processing time may be higher or lower than the actual intensity values.
A procedure for saturation curve generation can be found in the SAE specification SAE J443.
Typically, intensity verification occurs at the slowest saturating strip. Development work should be done to help make the strips saturate close to the same time. Most shot peening specs allow for this approach as long as the strips are repeatable (usually within .001″A) to the previous verification run.
As the impingement angle gets higher (closer to 90 degrees or perpendicular to the surface) intensity increases. The relationship is based on the sine of the angle of impingement; i.e. a 45 degree impingement angle intensity will be at ~70% of the intensity at 90 degrees.
No. Almen strips can only be re-used for the flapper peening process saturation curve development.
Yes. You can measure shot velocity with the ShotMeter G3 Particle Velocity Sensor.
No. You can actually hurt the fatigue life of a part by over shot peening the surface. Over peening causes excessive cold work and actually causes stress risers and crack initiation sites.
100% coverage is determined by visual inspection of the surface of a part. 125% coverage is 1.25 times the time to achieve 100% coverage.
Yes, the size distribution of the shot peening media is different on the MIL spec than the SAE. AMS-S-13165 outlines the size distribution for MIL spec shot, and SAE J444 outlines the size distribution for SAE cast steel shot, while SAE J442 outlines it for conditioned cut wire peening media.
Testing the hardness of media is accomplished by mounting media in an epoxy or phenolic metallurgical mount. The specimen is ground approx halfway through the shot diameter. It is polished and micro-hardness tested on either a Knoop or Vickers scale and then converted to Rockwell C scale.
Cut wire shot has a more consistent size and density. Because it does not break or crack, it will wear down over time. Typically it has a 10x longer life over cast steel shot. The initial investment in the shot is approx 3x more expensive.
New cast steel shot is tested by performing a sieve analysis on a Ro-Tap (i.e. SAE J444 or AMS 2431/1,2). A Ro-Tap is a device which shakes and taps test sieves. New cut wire media is typically tested by the measurement and precision weighing a sample (i.e. SAE J442 or AMS 2431/3,4, and 8). In-process media (media being used in a machine) is typically inspected by performing a sieve analysis with a Ro-Tap.
Yes, non-round media can cause cuts and stress risers in the surface of a part and can create a location for a crack to propagate from.
A single nozzle robotic machine can be as fast, or even faster than a multi nozzle machine because of target efficiency. The single nozzle can be programmed to precisely strike the surface of the part with very consistent impingement angles and programs can be tuned to prove consistent coverage over the entire surface of the part. This increases target efficiency and reduces wear and tear on a machine caused by overspray.
TBC stands for Tensile Bolting Cloth. MG stands for Market Grade. TBC and MG wire cloth are both used in media screening systems. MG uses thicker wires which help in longevity of screens, but there is less open area on a screen and therefore less media can get through. Contact a Progressive Surface customer service representative to see what will work best for you.
A US standard test sieve is used for testing and sizing the media. An #80 MG, TBC, and test sieve are not the same and cannot be used interchangeably. See the Sweco screen chart for details.
You can improve the surface finish of a part with shot peening. Many things that affect the ability to do this are initial surface roughness, media diameter, and intensity.
NADCAP stands for the National Aerospace and Defense Contractors Accreditation Program. The goal of the program is to coordinate industry wide standards for special processes. Having industry wide standards makes it easier for contractors to produce parts for several manufacturers without having the burden of going through complicated audits for each manufacturer individually.
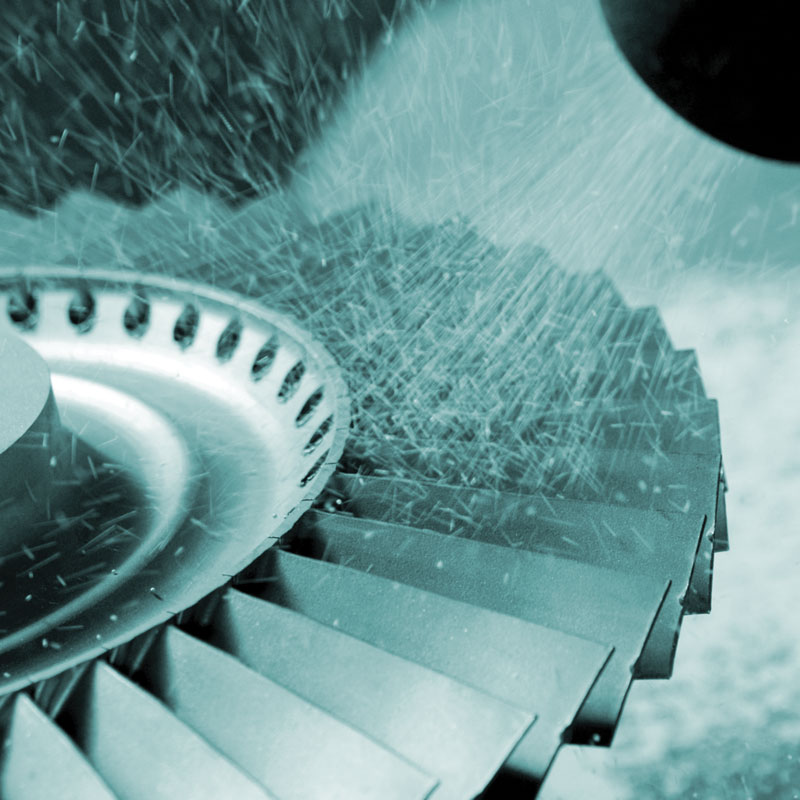